Track rollers play a role in reducing ground pressure and minimizing damage to sensitive surfaces in the following ways:
Weight Distribution: Track rollers, along with other undercarriage components, help distribute the weight of the excavator over a larger surface area. This distribution of weight helps reduce the ground pressure exerted by the machine. By spreading the load, the pressure per unit area decreases, minimizing the impact on the ground and sensitive surfaces.
Ground Contact Area: The track rollers, in conjunction with other undercarriage components, increase the contact area between the tracks and the ground. A larger contact area helps distribute the machine’s weight more evenly, reducing the ground pressure exerted at any specific point. This helps mitigate damage to sensitive surfaces, such as grass, asphalt, or fragile terrain.
Track Design: The design of track rollers and their interaction with the tracks can contribute to reducing ground pressure. Some track designs incorporate features like broader tracks, wider track shoes, or specialized track pads with increased surface area. These design elements help distribute the weight more effectively, minimizing the pressure exerted on the ground.
Track Tension: Proper track tension, which is facilitated by the track rollers, is crucial for reducing ground pressure. Overly loose tracks can sink into the ground, increasing the ground pressure at specific points, potentially causing damage. On the other hand, excessively tight tracks can create unnecessary strain on the undercarriage and increase ground pressure. The track rollers help maintain optimal track tension, ensuring the machine operates with reduced ground pressure.
Ground Surface Preservation: By reducing ground pressure and minimizing damage to sensitive surfaces, track rollers help preserve the integrity and aesthetics of the ground. This is particularly important in applications such as landscaping, construction in urban areas, or working on delicate terrain where surface damage needs to be minimized.
It’s important to note that while track rollers contribute to reducing ground pressure, other factors such as the overall weight of the machine, track design, track shoe type, and operator skill also play a role. Additionally, proper machine operation techniques, such as avoiding excessive speed or sudden turns, can further help minimize ground pressure and protect sensitive surfaces.
Are there any aftermarket options available for track rollers?
Yes, there are aftermarket options available for track rollers. Aftermarket track rollers are alternative products that are manufactured by companies other than the original equipment manufacturer (OEM). These aftermarket options are designed to fit and function as replacements for the track rollers of various excavator models.
Here are some key points to consider regarding aftermarket track rollers:
Cost: Aftermarket track rollers are often priced competitively compared to OEM track rollers. They can offer cost savings, making them an attractive option for equipment owners and operators.
Quality and Compatibility: The quality and compatibility of aftermarket track rollers can vary depending on the manufacturer. It is important to choose reputable aftermarket suppliers that produce high-quality products designed to meet or exceed industry standards. track rollers excavator Proper research and supplier evaluation can help ensure compatibility and performance.
Warranty and Support: Some aftermarket suppliers offer warranties and customer support for their products. It’s advisable to review the warranty terms and conditions provided by the supplier to understand the level of support available.
Availability and Selection: Aftermarket track rollers are available for a wide range of excavator models and brands. This allows equipment owners to find suitable replacements for their specific machine requirements. However, it’s important to verify the compatibility and specifications of the aftermarket track rollers to ensure they meet the machine’s needs.
Performance and Durability: The performance and durability of aftermarket track rollers can vary depending on the manufacturer and the specific product. It is advisable to research customer reviews, product specifications, and reputation of the aftermarket supplier before making a purchase.
Installation and Maintenance: Aftermarket track rollers can be installed and maintained using similar procedures as OEM track rollers. It is essential to follow the manufacturer’s instructions and recommendations to ensure proper installation and maintenance practices.
When considering aftermarket track rollers, it is recommended to consult with industry professionals, such as equipment technicians or dealers, who have experience with aftermarket products. They can provide guidance and advice based on their expertise and knowledge of the specific equipment and aftermarket options available in the market.
Overall, aftermarket track rollers can be a viable option for equipment owners seeking cost-effective alternatives to OEM track rollers. However, thorough research, supplier evaluation, and consideration of factors such as quality, compatibility, warranty, and support are crucial for making informed decisions.
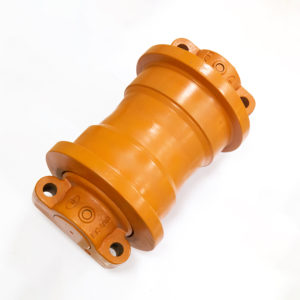