Is used in conjunction with an air-operated diaphragm pump to increase feed pump pressure at predetermined intervals during the filter press filling cycle. This initial layer becomes the filtering media, improving the filterability of the incoming slurry. This system can be combined with a new Met-Chem Filter Press, a used unit, or even your own existing press. Filter presses work on the principle of slurry being pumped into the machine so that solids are distributed evenly during the fill cycle.
Filter Press Application Industry
With a fully automatic filter press from Ton’s Per Hour, Inc., you are guaranteed maximum reliability as well as the most efficient solids removal and water recovery available in the industry. A TPH filter press will provide you with the high throughput and dependability you require for both dry stack fine tailings/refuse and dry solid concentrate duties. TPH has recently installed filter presses in critical industries such as coal, silica, limestone, granite, iron ore, gold mining, spherical graphite, ash, and others.
All three are due to the cakes being extremely sticky due to the wastewater containing blood from a nearby slaughterhouse. As a result, a small amount of crushed stone filter aid is used to improve dewatering, increasing the wear on the filter cloths significantly. Despite this increased wear, the plant has only had to replace approximately 30 cloths and one set of scraper blades in nearly three years of operation.
To compensate for the increase in flow resistance caused by pore clogging, the filtration must be operated by increasing the pressure difference. The filtration rate is primarily influenced by the filtrate’s viscosity as well as the resistance of the filter plate and cake. When filtrate passes through the filter plate, solids deposition occurs, increasing cake thickness and thus Rc, while Rf is assumed to be constant. By calculating the flow rate of filtration through the cake and filter medium, the flow resistance from them can be studied. The filter cake accumulates and thickens as the slurry is pumped through the membranes.
Filter Press Types
A filter press’s centre feed pipe assembly should last for many years, just like any other type of plumbing. However, if the material used in the centre feed pipe assembly is not strong enough to withstand the corrosiveness of the solution running through the press, the centre feed pipe assembly will corrode. ErtelAlsop has been a pioneer in the production of depth filter media and liquid filtration machinery since the 1920s, and is your one-stop shop for all depth filtration and liquid processing products. ErtelAlsop’s clientele includes customers who have been purchasing from us for over 80 years.
We can provide a compact layout and a light weight support frame design by sealing the filter plate pack. Polypropylene filter plates are used because of their chemical resistance and light weight. Fully automatic control system The Automatic, Pendant Controlled Plate Shifter is attached to the press sidebars and controlled by a hand-held control. During the cleaning process, the plate shifter allows for easy movement of the filter plates. This is especially true when using a large capacity press with large, heavy plates. Skid-Mounted Precoat Stations are specifically designed to work with any oil filter press.
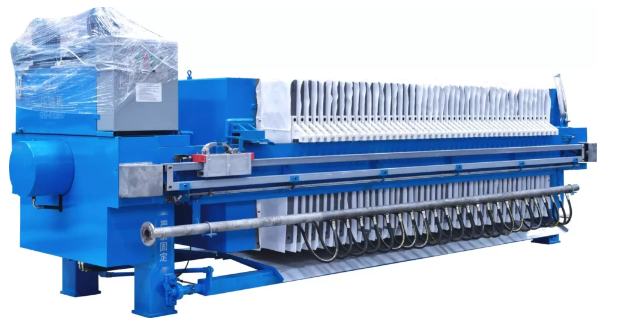
Today, the company’s Rotary Press technology is used in over 450 industrial and municipal installations around the world. The FullAuto Filter Press was recently introduced to North America by the company. This new technology, which is well known in the rest of the world, enables Fournier to provide a coherent and appropriate solution to customers facing a dewatering challenge.
The basic precoating procedure entails mixing a slurry of filter aid, which is typically a combination of water and Diatomaceous Earth. After that, the slurry is pumped into the Filter Press and recirculated into the holding tank. This process is repeated until the liquid appears clear or until the desired depth of precoat is reached. Special applications, such as pharmaceuticals and food processing, may require a different feed style. Center feed is the standard, but any corner feed is available. The discharge/air blow-down piping can be operated manually or automatically.